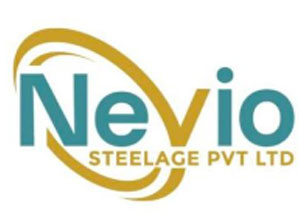
Our range of industrial flanges are ideal for application in diverse industry for high pressure and temperature applications. These flanges are designed with precision for easy installation. Apart from standard flanges, we also offer custom designed flanges to meet the specific application requirements of the customers.
Products is acknowledged as a manufacturer, exporter & suppliers of Slip On Flange & Stainless steel Flanges (Gr. 304, 304L, 316, 316L) available in a variety or grades, materials, and finishes, in metric and inch sizes. These Slip On Flange are manufacture in different Material of Flanges like SORF Flanges, Carbon Steel Slip On Flanges, Stainless Steel Slip On Flanges, Alloy Steel Slip On Flanges, Duplex Steel Slip On Flanges, Inconel Slip On Flanges, Monel Slip On Flanges, Hastelloy Slip On Flanges, Copper Nickel Slip On Flanges in India & Asia, conform to Slip On specifications.
The flange is slipped over the pipe and then welded both inside and outside to provide sufficient Strength and prevent leakage. This flange is used in preference to weld necks by many users because of its lower cost and the fact that less accuracy is required when cutting pipe to length.Drilling | |||||||||
---|---|---|---|---|---|---|---|---|---|
Nominal Bore | Dia.(D) | Thick.(E) | Dia.(F) | Dia.(B) | Dia.(A) | Height1(H) | Nbr | Holes | Dia.(C) |
1/2″ | 90 | 9.6 | 35.05 | 30 | 22.2 | 14 | 4 | 15.87 | 60.3 |
3/4″ | 100 | 11.2 | 42.93 | 38 | 27.7 | 14 | 4 | 15.87 | 69.9 |
1″ | 110 | 12.7 | 50.80 | 49 | 34.5 | 16 | 4 | 15.87 | 79.4 |
1 1/4″ | 115 | 14.3 | 63.50 | 59 | 43.2 | 19 | 4 | 15.87 | 88.9 |
1 1/2″ | 125 | 15.9 | 73.15 | 65 | 49.5 | 21 | 4 | 15.87 | 98.4 |
2″ | 150 | 17.5 | 91.95 | 78 | 61.9 | 24 | 4 | 19.05 | 120.7 |
2 1/2″ | 180 | 20.7 | 104.65 | 90 | 74.6 | 27 | 4 | 19.05 | 139.7 |
3″ | 190 | 22.3 | 127.00 | 108 | 90.7 | 29 | 4 | 19.05 | 152.4 |
3 1/2″ | 215 | 22.3 | 139.70 | 122 | 103.4 | 30 | 8 | 19.05 | 177.8 |
4″ | 230 | 22.3 | 157.22 | 135 | 116.1 | 32 | 8 | 19.05 | 190.5 |
5″ | 255 | 22.3 | 185.67 | 164 | 143.8 | 35 | 8 | 22.22 | 215.9 |
6″ | 280 | 23.9 | 215.90 | 192 | 170.7 | 38 | 8 | 22.22 | 241.3 |
8″ | 345 | 27.0 | 269.75 | 246 | 221.5 | 43 | 8 | 22.22 | 298.5 |
10″ | 405 | 28.6 | 323.85 | 305 | 276.2 | 48 | 12 | 25.40 | 362.0 |
12″ | 485 | 30.2 | 381.00 | 365 | 327.0 | 54 | 12 | 25.40 | 431.8 |
14″ | 535 | 33.4 | 412.75 | 400 | 359.2 | 56 | 12 | 28.57 | 476.3 |
16″ | 595 | 35.0 | 469.90 | 457 | 410.5 | 62 | 16 | 28.57 | 539.8 |
18″ | 635 | 38.1 | 533.40 | 505 | 461.8 | 67 | 16 | 31.75 | 577.9 |
20″ | 700 | 41.3 | 584.20 | 559 | 513.1 | 71 | 20 | 31.75 | 635.0 |
24″ | 815 | 46.1 | 692.15 | 663 | 616.0 | 81 | 20 | 34.92 | 74 |
Scope of Alloy Pipe Impex nickel flanges are perfect for application in various industry
for high weight and temperature applications. These flanges are composed with exactness for
simple establishment. Aside from standard flanges, we likewise offer hand crafted nickel
flanges to meet the particular application prerequisites of the clients.
Item Code: 7219
Port Of Dispatch: Any
Production Capacity: Ready Stock
Packaging Details: As Per Customer Requirment
Material Standard | ANSI B16.5, ASTM A182, ASTM A351, ASTM A105 |
Product Type | Bars, Pellets, Rods |
Grades | Nickel 200 , Nickel 201 |
Material Grade | All standard grades |
Diameter | All standard sizes |
Material | Nickel Alloy |
Size | >30 inch |
We are offering Monel Alloy Flanges to our clients. Contact us for more consultation and orders.
Production Capacity: 70,000 Metric Tons
Port Of Dispatch: Any
Delivery Time: Ready Stock
Packaging Details: As Per Buyer's Requirement
Size | 20-30 inch, 5-10 inch, 1-5 inch, >30 inch, 0-1 inch, 10-20 inch |
Material Standard | ASTM A351, ANSI B16.5, ASTM A182, ASTM A105 |
Condition | New |
Color | Any |
Material | Monel Alloy |
Inconel flanges can withstand high temperatures, making them ideal for applications in environments with extreme heat, such as gas turbines and exhaust systems.
The nickel content in Inconel provides excellent resistance to oxidation and corrosion, even in harsh environments like seawater, acidic, and alkaline environments.
Inconel forms a protective oxide layer when exposed to high temperatures, which helps to prevent further oxidation.
Inconel 600:
Good oxidation and corrosion resistance at higher temperatures.
Commonly used in chemical and food processing, nuclear engineering, and the aerospace industry.
Specification | Details |
---|---|
Material Grades | Inconel 600, Inconel 625, Inconel 718 |
Standards | ASME B16.5, ASME B16.47, ASTM B564, ASTM B472, DIN 2632, DIN 2633 |
Sizes | 1/2" to 48" (Nominal Pipe Size) |
Pressure Ratings | 150#, 300#, 400#, 600#, 900#, 1500#, 2500# |
Types of Flanges | Weld Neck, Slip-On, Blind, Socket Weld, Lap Joint, Threaded, Orifice, Long Weld Neck |
Temperature Range | -200°C to 1200°C |
Corrosion Resistance | Excellent in various aggressive environments including oxidizing and reducing conditions |
Applications | Aerospace, Chemical Processing, Marine, Power Generation, Oil & Gas |
Mechanical Properties | Yield Strength: 65-105 ksi, Tensile Strength: 95-150 ksi |
Chemical Composition | Varies by grade; common elements include Nickel (58-72%), Chromium (14-23%), Molybdenum (up to 10%) |
Manufacturing Process | Forged, Heat-treated, Machined |
Testing and Quality Control | Hydrostatic Testing, Ultrasonic Testing, Radiography, Magnetic Particle Inspection |
Surface Finish | Smooth, Rust-proof Oil, Black, Galvanized, as per customer requirement |
Certification | Mill Test Certificate (MTC) according to EN 10204 3.1/3.2 |
Hastelloy is a high-performance nickel-molybdenum-chromium superalloy known for its exceptional resistance to corrosion, especially in harsh chemical environments. Hastelloy flanges are critical components in industries that demand materials capable of withstanding extreme conditions, including high temperatures and corrosive substances.
Hastelloy C-276:
Excellent resistance to pitting, stress-corrosion cracking, and oxidizing atmospheres up to 1900°F (1038°C).
Commonly used in chemical processing, pollution control, and waste treatment.
Hastelloy C-22:
Superior resistance to corrosion, especially in oxidizing environments.
Widely used in pharmaceutical, food processing, and petrochemical industries.
Specification | Details |
---|---|
Material Grades | Hastelloy C-276, Hastelloy C-22, Hastelloy B-2 |
Standards | ASME B16.5, ASME B16.47, ASTM B564, ASTM B472, DIN 2632, DIN 2633 |
Sizes | 1/2" to 48" (Nominal Pipe Size) |
Pressure Ratings | 150#, 300#, 400#, 600#, 900#, 1500#, 2500# |
Types of Flanges | Weld Neck, Slip-On, Blind, Socket Weld, Lap Joint, Threaded, Orifice, Long Weld Neck |
Temperature Range | -200°C to 1250°C |
Corrosion Resistance | Excellent in various aggressive environments including oxidizing and reducing conditions |
Applications | Chemical Processing, Pharmaceuticals, Power Generation, Marine, Oil & Gas |
Mechanical Properties | Yield Strength: 35-70 ksi, Tensile Strength: 100-150 ksi |
Chemical Composition | Varies by grade; common elements include Nickel (57-70%), Chromium (14-22%), Molybdenum (up to 30%) |
Manufacturing Process | Forged, Heat-treated, Machined |
Testing and Quality Control | Hydrostatic Testing, Ultrasonic Testing, Radiography, Magnetic Particle Inspection |
Surface Finish | Smooth, Rust-proof Oil, Black, Galvanized, as per customer requirement |
Certification | Mill Test Certificate (MTC) according to EN 10204 3.1/3.2 |
Super Duplex stainless steel is a type of advanced stainless steel known for its excellent corrosion resistance, high strength, and resistance to stress corrosion cracking. It is composed of a mixed microstructure of austenite and ferrite, typically in a 50/50 ratio.
Super Duplex 2507 (UNS S32750):
Contains approximately 25% chromium, 4% molybdenum, and 7% nickel.
Excellent general corrosion resistance and strength.
Super Duplex 32760 (UNS S32760):
Similar composition to 2507 with the addition of tungsten for improved pitting resistance.
Often used in oil and gas applications.
Specification | Details |
---|---|
Material Grades | Super Duplex 2507 (UNS S32750), Super Duplex 32760 (UNS S32760) |
Standards | ASME B16.5, ASME B16.47, ASTM A182, ASTM A240, DIN 2632, DIN 2633 |
Sizes | 1/2" to 48" (Nominal Pipe Size) |
Pressure Ratings | 150#, 300#, 400#, 600#, 900#, 1500#, 2500# |
Types of Flanges | Weld Neck, Slip-On, Blind, Socket Weld, Lap Joint, Threaded, Orifice, Long Weld Neck |
Temperature Range | -50°C to 300°C (can vary depending on specific grade and application) |
Corrosion Resistance | Excellent in various aggressive environments including seawater and chlorides |
Applications | Oil and Gas, Chemical Processing, Marine, Power Generation, Desalination |
Mechanical Properties | Yield Strength: 80-110 ksi, Tensile Strength: 115-135 ksi |
Chemical Composition | Chromium (24-26%), Nickel (6-8%), Molybdenum (3-4%), Nitrogen (0.24-0.32%), others as specified |
Manufacturing Process | Forged, Heat-treated, Machined |
Testing and Quality Control | Hydrostatic Testing, Ultrasonic Testing, Radiography, Magnetic Particle Inspection |
Surface Finish | Smooth, Rust-proof Oil, Black, Galvanized, as per customer requirement |
Certification | Mill Test Certificate (MTC) according to EN 10204 3.1/3.2 |
Duplex flanges are made from an austenitic-ferritic stainless steel, which was designed to deliver higher strength and corrosion resistance than other 300 series stainless steel flanges. It helps users to avoid stress corrosion, cracking that is typically seen with 316 and 317. The advantages of duplex stainless steel – higher strength, better fatigue properties, high resistance to chloride stress corrosion cracking etc.
Standard | ASTM A182 |
Type | Weldneck, Slipon, Blind, Socketweld |
Grade | F51 (31803), F53 (32750), F55 (32760), F61 (32261) |
Size | 0.5” to 12” |
Class | 150#, 300#, 600#, 900#, 1500# |
Stainless steel Flanges are widely used in both domestic and industrial applications because of the various benefits it offers. It is resistant to corrosion and temperature and appearance is good. The flanges made of stainless steel offers all these benefits and many more. Stainless steel flanges are important in industries like transport, gas, water, food, beverage, chemical process etc where piping is required these flanges are used for connections. Flanges are important part of the piping connection and also provides easy access for cleaning, inspection or modification.
Standard | ASTM A182 |
Type | Weldneck, Slipon, Blind, Socketweld |
Grade | 304, 304L, 304H, 310, 310S, 316, 316L, 316ti, 317, 317L, 321, 347, 904L |
Size | 0.5” to 24” |
Class | 150#, 300#, 600#, 900#, 1500# |
Alloy steel flanges offer high tensile and yield strength, making them suitable for high-pressure applications.
Durability:
Excellent resistance to wear and tear, providing long service life even in harsh conditions.
Temperature Resistance:
Capable of withstanding high temperatures without losing strength or integrity.
A182 F1:
Contains molybdenum for increased strength and corrosion resistance.
Used in high-temperature service applications.
A182 F5:
Contains chromium and molybdenum, offering good resistance to oxidation and corrosion.
Suitable for high-temperature service in oil refineries and power plants.
A182 F9:
Contains higher chromium and molybdenum content for better corrosion and oxidation resistance.
Ideal for high-pressure and high-temperature applications.
Specification | Details |
---|---|
Material Grades | A182 F1, A182 F5, A182 F9, A182 F11, A182 F22 |
Standards | ASME B16.5, ASME B16.47, ASTM A182, ASTM A105, DIN 2632, DIN 2633 |
Sizes | 1/2" to 48" (Nominal Pipe Size) |
Pressure Ratings | 150#, 300#, 400#, 600#, 900#, 1500#, 2500# |
Types of Flanges | Weld Neck, Slip-On, Blind, Socket Weld, Lap Joint, Threaded, Orifice, Long Weld Neck |
Temperature Range | -29°C to 593°C (can vary depending on specific grade and application) |
Corrosion Resistance | Enhanced resistance to oxidation, sulfidation, and other forms of corrosion |
Applications | Power Generation, Petrochemical, Oil and Gas, Chemical Processing |
Mechanical Properties | Yield Strength: 30-80 ksi, Tensile Strength: 60-100 ksi |
Chemical Composition | Chromium (1-9%), Molybdenum (0.5-1%), Nickel, Vanadium, Carbon, Manganese, Silicon |
Manufacturing Process | Forged, Heat-treated, Machined |
Testing and Quality Control | Hydrostatic Testing, Ultrasonic Testing, Radiography, Magnetic Particle Inspection |
Surface Finish | Smooth, Rust-proof Oil, Black, Galvanized, as per customer requirement |
Certification | Mill Test Certificate (MTC) according to EN 10204 3.1/3.2 |
Carbon Steel Flanges are pipe connectors that join two pieces of piping together. They are made using carbon steel material and contain a raised lip or rim that ensures a strong bond is formed between the pipes by welding them together. Furthermore, they are designed to support greater pressure due to their stronger construction. These metallic connections also provide moderate corrosion resistance, making them ideal for industrial & general purpose applications.
Standard | ASTM A105 |
Type | Weldneck, Slipon, Blind, Socketweld |
Size | 0.5” to 24” |
Class | 150#, 300#, 600#, 900#, 1500# |
Aluminum flanges are significantly lighter than steel and other metal flanges, making them easier to handle and install.
Excellent resistance to corrosion, especially in environments exposed to moisture and chemicals. This makes them suitable for marine and chemical applications.
6061:
Known for its excellent mechanical properties and weldability. Suitable for structural applications.
5083:
Offers high strength and exceptional resistance to seawater corrosion. Commonly used in marine applications.
7075:
High strength and good fatigue resistance. Used in aerospace and high-stress applications.
Specification | Details |
---|---|
Material Grades | 6061, 5083, 7075 |
Standards | ASME B16.5, ASME B16.47, ASTM B247, DIN 2632, DIN 2633 |
Sizes | 1/2" to 48" (Nominal Pipe Size) |
Pressure Ratings | 150#, 300#, 400#, 600#, 900#, 1500# |
Types of Flanges | Weld Neck, Slip-On, Blind, Socket Weld, Lap Joint, Threaded, Orifice, Long Weld Neck |
Temperature Range | -270°C to 150°C (can vary depending on specific grade and application) |
Corrosion Resistance | Excellent, particularly in marine and chemical environments |
Applications | Marine, Chemical Processing, Aerospace, Automotive, Electrical |
Mechanical Properties | Yield Strength: 35-80 ksi, Tensile Strength: 60-90 ksi |
Chemical Composition | Varies by grade; common elements include Aluminum (90-99%), Magnesium (0.8-1.2%), Silicon (0.4-0.8%) |
Manufacturing Process | Forged, Extruded, Machined |
Testing and Quality Control | Hydrostatic Testing, Ultrasonic Testing, Radiography, Dimensional Inspection |
Surface Finish | Smooth, Anodized, Polished, as per customer requirement |
Certification | Mill Test Certificate (MTC) according to EN 10204 3.1/3.2 |
Titanium flanges are highly sought after in various industries due to their exceptional properties, such as high strength-to-weight ratio, corrosion resistance, and biocompatibility. They are particularly useful in environments where both strength and resistance to harsh conditions are required.
High Strength-to-Weight Ratio:
Titanium flanges provide excellent strength while being significantly lighter than steel flanges, making them ideal for applications where weight reduction is crucial.
Corrosion Resistance:
Outstanding resistance to corrosion in seawater, acidic environments, and other aggressive chemicals. This makes them suitable for marine, chemical processing, and offshore applications.
Grade 2 (Commercially Pure Titanium):
Known for its excellent corrosion resistance, weldability, and ductility. Used in chemical processing, marine, and medical applications.
Grade 5 (Ti-6Al-4V):
The most commonly used titanium alloy, known for its high strength, lightweight, and excellent corrosion resistance. Used in aerospace, medical, and high-performance engineering applications.
Specification | Details |
---|---|
Material Grades | Grade 2, Grade 5 (Ti-6Al-4V), Grade 7, Grade 12 |
Standards | ASME B16.5, ASME B16.47, ASTM B381, DIN 2632, DIN 2633 |
Sizes | 1/2" to 48" (Nominal Pipe Size) |
Pressure Ratings | 150#, 300#, 400#, 600#, 900#, 1500# |
Types of Flanges | Weld Neck, Slip-On, Blind, Socket Weld, Lap Joint, Threaded, Orifice, Long Weld Neck |
Temperature Range | -250°C to 400°C (can vary depending on specific grade and application) |
Corrosion Resistance | Excellent, particularly in seawater, acidic, and aggressive chemical environments |
Applications | Aerospace, Chemical Processing, Marine, Medical, Power Generation |
Mechanical Properties | Yield Strength: 40-130 ksi, Tensile Strength: 50-140 ksi |
Chemical Composition | Varies by grade; common elements include Titanium (90-99%), Aluminum, Vanadium, Palladium, Molybdenum |
Manufacturing Process | Forged, Extruded, Machined |
Testing and Quality Control | Hydrostatic Testing, Ultrasonic Testing, Radiography, Dimensional Inspection |
Surface Finish | Smooth, Polished, Pickled, as per customer requirement |
Certification | Mill Test Certificate (MTC) according to EN 10204 3.1/3.2 |
Nimonic flanges are crucial components in various high-temperature and high-stress applications, renowned for their exceptional heat and corrosion resistance. Nimonic alloys, which are nickel-based superalloys, exhibit remarkable mechanical properties even at elevated temperatures.
High Temperature Resistance:
Nimonic flanges can withstand extreme temperatures, making them ideal for applications in aerospace, gas turbine engines, and industrial furnaces.
Excellent Mechanical Properties:
These alloys retain their mechanical strength even at elevated temperatures, offering good creep and rupture resistance.
Nimonic 75:
Offers good mechanical properties and corrosion resistance at high temperatures. Used in gas turbine engines and industrial heating applications.
Nimonic 80A:
Provides excellent creep and oxidation resistance at temperatures up to 815°C. Widely used in gas turbine components and high-temperature applications.
Nimonic 90:
Known for its high strength and creep resistance at temperatures up to 950°C. Commonly used in aircraft parts and industrial furnace components.
Specification | Details |
---|---|
Material Grades | Nimonic 75, Nimonic 80A, Nimonic 90 |
Standards | ASTM B637, AMS 5666, BS HR 403, DIN 17752 |
Sizes | 1/2" to 48" (Nominal Pipe Size) |
Pressure Ratings | 150#, 300#, 400#, 600#, 900#, 1500# |
Types of Flanges | Weld Neck, Slip-On, Blind, Socket Weld, Lap Joint, Threaded, Orifice, Long Weld Neck |
Temperature Range | Up to 950°C (varies depending on alloy and application) |
Corrosion Resistance | Excellent resistance to oxidation and corrosion in high-temperature environments |
Applications | Aerospace, Power Generation, Industrial Furnaces, Oil and Gas |
Mechanical Properties | Yield Strength: 300-600 MPa, Tensile Strength: 700-1000 MPa |
Chemical Composition | Varies by grade; common elements include Nickel (50-70%), Chromium (15-21%), Cobalt (10-20%), Titanium (1-2%) |
Manufacturing Process | Forged, Heat-treated, Machined |
Testing and Quality Control | Non-destructive Testing (NDT), Dimensional Inspection, Chemical Analysis, Mechanical Testing |
Surface Finish | Smooth, Pickled, Passivated, as per customer requirement |
Certification | Mill Test Certificate (MTC) according to EN 10204 3.1/3.2 |
Copper flanges play a vital role in various industrial applications due to the unique properties of copper, such as excellent thermal and electrical conductivity, corrosion resistance, and antimicrobial properties. These flanges are commonly used in plumbing systems, HVAC (heating, ventilation, and air conditioning) systems, and electrical installations. Below is an overview of copper flanges, including their specifications, characteristics, and applications.
Copper Alloys: Copper alloys, such as brass (copper-zinc alloy) and bronze (copper-tin alloy), are often used in flange manufacturing to enhance specific properties like strength, corrosion resistance, and machinability.
Specification | Details |
---|---|
Material | Copper, Copper Alloys (Brass, Bronze) |
Standards | ASTM B16.5, ASTM B62, ASTM B584, ASME B16.24, ASME B16.5, DIN 86029 |
Sizes | 1/2" to 48" (Nominal Pipe Size) |
Pressure Ratings | 150#, 300#, 400#, 600#, 900#, 1500# |
Types of Flanges | Weld Neck, Slip-On, Blind, Socket Weld, Threaded |
Temperature Range | Up to 250°C (varies depending on specific copper alloy) |
Corrosion Resistance | Excellent resistance to corrosion in atmospheric and aqueous environments |
Applications | Plumbing Systems, HVAC Systems, Electrical Installations, Industrial Equipment, Marine |
Manufacturing Process | Forged, Machined, Cast |
Testing and Quality Control | Visual Inspection, Dimensional Inspection, Chemical Analysis, Pressure Testing |
Surface Finish | Smooth, Polished, as per customer requirement |
Certification | Mill Test Certificate (MTC) according to EN 10204 3.1/3.2 |
Brass flanges are widely used in various industries due to the unique properties of brass, such as corrosion resistance, machinability, and aesthetic appeal. These flanges are commonly employed in plumbing systems, marine applications, and decorative fittings. Below is an overview of brass flanges, including their specifications, characteristics, and applications.
Corrosion Resistance:
Brass exhibits excellent corrosion resistance, particularly in non-saline environments, making brass flanges suitable for plumbing and decorative applications.
Alpha Brass:
Contains more than 63% copper and is often used for general-purpose applications due to its good strength and corrosion resistance.
Alpha-Beta Brass:
Contains between 55% to 63% copper and exhibits improved machinability compared to alpha brass.
Specification | Details |
---|---|
Material | Brass (Alpha Brass, Alpha-Beta Brass) |
Standards | ASTM B16.5, ASTM B584, ASME B16.24, ASME B16.5, DIN 86029 |
Sizes | 1/2" to 48" (Nominal Pipe Size) |
Pressure Ratings | 150#, 300#, 400#, 600#, 900#, 1500# |
Types of Flanges | Weld Neck, Slip-On, Blind, Socket Weld, Threaded |
Temperature Range | Up to 250°C (varies depending on specific brass alloy) |
Corrosion Resistance | Excellent resistance to corrosion in non-saline environments |
Applications | Plumbing Systems, Marine Applications, Decorative Fittings, Automotive, Instrumentation |
Manufacturing Process | Forged, Machined, Cast |
Testing and Quality Control | Visual Inspection, Dimensional Inspection, Chemical Analysis, Pressure Testing |
Surface Finish | Smooth, Polished, as per customer requirement |
Certification | Mill Test Certificate (MTC) according to EN 10204 3.1/3.2 |