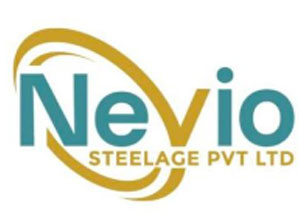
We also stock Bar, Hexagon, Square, Round products in various dimensions and grades. We stock Stainless Steel, Carbon and Alloy specialty steels supplied in the as rolled, annealed and normalized conditions. We offer cut to size and heat treatment through our service center.
User Industries : Chemicals, Fats, & Fertilizers, Sugar Mills & Distilleries, Cement Industries, Ship Builders, Paper Industries, Pumps, Petrochemicals, Oil & Natural Gas Organization in terms of the specific materials, Technology, Finance & Personal.Bar Standard | ASTM A276, ASTM A479, AMS 5513, AMS 5511, AMS 5647 |
---|---|
Bar Dimensions | EN, DIN, JIS, ASTM, BS, ASME, AISI |
Round bar size | Diameter: 3-~800mm |
Hex Bar size | 2-100mm A/F |
Flat bar size | Thickness: 2 -100mm |
Width: 10 to 500mm | |
Square bar size | 4 to 100mm |
Angle bar size | 3mm*20mm*20mm~12mm*100mm*100mm |
Rectangular Bars Section | 3.0 to 12.0mm thickness |
Channel Bar | 80 x 40mm to 150 x 75mm section; 5.0 to 6.0mm thickness |
ASTM A276 Type Hollow Bar | 32mm OD x 16mm ID to 250mm OD x 200mm ID) |
Threaded Bar Billet Size | 1/2 to 495mm Diameter |
Rectangular Size | 33 x 30mm to 295 x 1066mm |
Hex Bars Finish | Cold (bright) drawn, centreless ground, hot rolled, smooth turned, peeled, slit rolled edge, hot rolled annealed, Rough Turned, Bright, Polish, Grinding, Centreless Ground & Black |
ASTM A276 Type Hollow Bar Tolerance | H8, H9, H10, H11, H12, H13K9, K10, K11, K12 or as per clients’ requirements |
SUS T-Bar Surface | Bright, Hot Rolled Pickled, Cold Drawn, Sand Blasting Finished, Polished, Hairline |
Rolled Stainless Steel Flat Bars Condition | Hardened & tempered, annealed |
ASTM A276 Type Cold Rolled Bar Technique | Stainless Steel Hot Rolled, Cold Drawn, Cold Rolled, Forged Round Bar, Rod |
Rod Processing | Bar cutting to 650mm |
Rounds Bar Form | Round, Rod, T-Bar, Channel Bar, Precision Ground Bar, Flat Bar, Square, Blocks, Round Rod, Rings, Hollow, Triangle, Rectangle, Hex (A/F), Threaded, Half Round Bar, Profiles, Billet, Ingot, I/H Bar, Forging etc. |
Our Stainless Steel Round bar conforms to NACE MR0175/ISO 15156 |
Round bar Cutting |
Products cut include Round bars, Flat bars, Hex bars, Square bars, Tubing and Hollow bars, Pipe, Angles, channels, Beams and Tees. Thickness range is 1/16″ to 28″ diameter |
Round bar Production Cutting |
We can provide production cutting for product diameters up to 4″. We utilize Amanda Production Equipment to achieve these precision cuts with tight tolerances. |
Round bar Polishing |
Products polished included all tubular products, with OD & ID polishing available, Round bars, Square bars, Hex & Flat bars, Angles, Uneven Leg Angles, beams, and other shapes. |
Nickel bar is a solid, straight round shape that is made of Nickel in a high-purity form. Nickel alloy bars are made with alloying correct chemical composition of different metals to get the uniform and required alloy. This chemical element is advantageous in many metallurgical applications. Nickel & Nickel alloy bars are tough, ferromagnetic, corrosion-resistant, ductile, malleable, and heat-resistant and are used in multiple industries like aerospace, defence, chemical, automotive, medical etc.
Standard | ASTM B160 / ASME SB 160 |
Size | 10mm – 150mm |
Grade | Nickel 200, Nickel 201, Monel 400, Monel K500, Inconel 625, Inconel 800, Inconel 825, Hastalloy C276, Alloy20 |
Type | Round |
Form | Straight , Coil |
Finish | Bright |
Length | Random Length, Custom cut length |
We are offering Monel Alloy Round Bar to our clients. Contact us for more consultation and orders.
Pay Mode Terms: L/C (Letter Of Credit),T/T (Bank Transfer),D/P,D/A
Production Capacity: 70,000 Metric Tons
Packaging Details: As Per Buyer's Requirement
Monel 400 (UNS N04400): The most widely used grade, known for its high strength and excellent resistance to corrosion, including sea water.
Monel K-500 (UNS N05500): A precipitation-hardenable alloy with added aluminum and titanium for increased strength and hardness.
Property | Monel 400 | Monel K-500 |
---|---|---|
Material | Nickel-Copper Alloy (UNS N04400) | Nickel-Copper Alloy (UNS N05500) |
Standard | ASTM B164 | ASTM B865 |
Grades Available | Monel 400 | Monel K-500 |
Composition | Ni: 63% min, Cu: 28-34%, Fe: 2.5% max | Ni: 63% min, Cu: 27-33%, Al: 2.30-3.15%, Ti: 0.35-0.85% |
Diameter Range | 6 mm to 300 mm | 6 mm to 300 mm |
Length | 3 meters to 6 meters (custom lengths available) | 3 meters to 6 meters (custom lengths available) |
Surface Finish | Black, polished, centerless ground | Black, polished, centerless ground |
Tensile Strength | 70 ksi (483 MPa) | 160 ksi (1100 MPa) |
Yield Strength | 28 ksi (193 MPa) | 115 ksi (790 MPa) |
Elongation | 35% | 20% |
Density | 8.80 g/cm³ | 8.44 g/cm³ |
Melting Point | 1300-1350°C | 1300-1350°C |
Corrosion Resistance | Excellent in seawater, acids, alkalis | Excellent in seawater, acids, alkalis |
Hardness (HB) | 75-90 HB | 150-200 HB |
Magnetic Properties | Non-magnetic | Non-magnetic |
Applications | Marine engineering, chemical processing, aerospace | Marine engineering, chemical processing, aerospace |
Weldability | Good | Fair |
Special Features | High strength, excellent corrosion resistance, retains strength at elevated temperatures | Precipitation hardenable, higher strength and hardness compared to Monel 400 |
Inconel 600: Nickel-chromium alloy with good oxidation and corrosion resistance at higher
temperatures.
Inconel 625: Nickel-chromium-molybdenum-niobium alloy known for excellent fatigue and thermal-fatigue
strength, oxidation, and corrosion resistance.
High-Temperature Strength: Inconel alloys maintain their strength and structural integrity at high
temperatures, making them suitable for extreme environments.
Oxidation and Corrosion Resistance: Inconel alloys exhibit excellent resistance to oxidation and
corrosion, even in aggressive environments.
Property | Specification |
---|---|
Material | Inconel (Nickel-based superalloy) |
Common Grades | Inconel 600, Inconel 625, Inconel 718, Inconel 825 |
Composition | Primarily Nickel and Chromium with Molybdenum, Iron, Cobalt, Niobium, etc. |
Diameter Range | Typically from 6mm to 200mm (varies per application) |
Tensile Strength | Varies by grade |
- Inconel 600: ~655 MPa | |
- Inconel 625: ~827 MPa | |
- Inconel 718: ~1241 MPa | |
- Inconel 825: ~586 MPa | |
Yield Strength | Varies by grade |
- Inconel 600: ~310 MPa | |
- Inconel 625: ~414 MPa | |
- Inconel 718: ~1034 MPa | |
- Inconel 825: ~241 MPa | |
Hardness | Varies by grade and heat treatment |
- Inconel 600: ~85 HRB | |
- Inconel 625: ~30 HRC | |
- Inconel 718: ~40 HRC | |
- Inconel 825: ~140 HB | |
Elongation | Varies by grade |
- Inconel 600: ~30% | |
- Inconel 625: ~30% | |
- Inconel 718: ~12% | |
- Inconel 825: ~30% | |
Temperature Resistance | Excellent |
- Inconel 600: up to 982°C | |
- Inconel 625: up to 982°C | |
- Inconel 718: up to 704°C | |
- Inconel 825: up to 540°C | |
Corrosion Resistance | Excellent in high-temperature and corrosive environments |
Creep Resistance | Excellent |
Formability | Good ductility, can be hot or cold worked |
Weldability | Generally good, but requires specific techniques to maintain properties |
Applications | Aerospace, power generation, chemical processing, marine, oil and gas |
Standard Specifications | AMS, ASTM, BS, DIN, ISO, etc. |
Hastelloy alloys primarily consist of nickel, with significant amounts of chromium, molybdenum, and
other elements such as tungsten, iron, cobalt, and sometimes aluminum and titanium to enhance
specific properties.
Hastelloy C-276: Nickel-molybdenum-chromium alloy with excellent resistance to pitting, stress
corrosion cracking, and oxidizing atmospheres up to 1040°C.
Hastelloy C-22: Nickel-chromium-molybdenum alloy with superior resistance to a wide range of
corrosive environments.
Hastelloy alloys maintain their mechanical properties at elevated temperatures, making them
suitable for high-temperature applications.
Property | Specification |
---|---|
Material | Hastelloy (Nickel-based superalloy) |
Common Grades | Hastelloy C-276, Hastelloy C-22, Hastelloy B-2, Hastelloy X |
Composition | Primarily Nickel, Chromium, Molybdenum, with Iron, Tungsten, Cobalt, etc. |
Diameter Range | Typically from 6mm to 200mm (varies per application) |
Tensile Strength | Varies by grade |
- Hastelloy C-276: ~800 MPa | |
- Hastelloy C-22: ~690 MPa | |
- Hastelloy B-2: ~760 MPa | |
- Hastelloy X: ~750 MPa | |
Yield Strength | Varies by grade |
- Hastelloy C-276: ~355 MPa | |
- Hastelloy C-22: ~310 MPa | |
- Hastelloy B-2: ~350 MPa | |
- Hastelloy X: ~340 MPa | |
Hardness | Varies by grade and heat treatment |
- Hastelloy C-276: ~200 HB | |
- Hastelloy C-22: ~180 HB | |
- Hastelloy B-2: ~187 HB | |
- Hastelloy X: ~220 HB | |
Elongation | Varies by grade |
- Hastelloy C-276: ~40% | |
- Hastelloy C-22: ~50% | |
- Hastelloy B-2: ~40% | |
- Hastelloy X: ~50% | |
Temperature Resistance | Excellent |
- Hastelloy C-276: up to 1040°C | |
- Hastelloy C-22: up to 1250°C | |
- Hastelloy B-2: up to 870°C | |
- Hastelloy X: up to 1200°C | |
Corrosion Resistance | Exceptional in both oxidizing and reducing environments |
Creep Resistance | Good |
Formability | Good ductility, can be hot or cold worked |
Weldability | Generally good, but requires specific techniques to maintain properties |
Applications | Chemical processing, aerospace, power generation, marine, oil and gas |
Standard Specifications | ASTM B574, ASME SB574, DIN 17752, ISO 9723, etc. |
Super Duplex stainless steel Bars are based around an alloying addition of 25% chromium, whereas Duplex stainless steels are based around an alloying addition of 22% chromium. By increasing the chromium content, the level of pitting corrosion resistance is also increased. As the duplex name suggests, this family of alloys have a microstructure made up of both austenitic and ferritic grains of steel and widely used in marine, oil & gas production, shipping & coastal developments.
Standard | ASTM A276 / ASME SA 276 |
Size | 10mm – 150mm |
Grade | F51 (31803), F53 (32750), F55 (32760), F61 (32205) |
Type | Round, Square, Hex |
Form | Straight , Coil |
Finish | Bright |
Length | upto 6000mm, Cut Length |
Duplex stainless steels typically contain approximately equal amounts of ferrite and austenite,
with chromium (usually 20-28%), nickel (1-9%), molybdenum (0.05-5%), and nitrogen as primary
alloying elements.
Duplex 2205 (UNS S31803/S32205): Widely used grade with good general corrosion resistance and
high strength.
High Strength: Duplex stainless steels have higher yield strength compared to standard austenitic
stainless steels.
Corrosion Resistance: Excellent resistance to a wide range of corrosive environments, including
chloride stress corrosion cracking and pitting.
Property | Specification |
---|---|
Material | Duplex Stainless Steel |
Common Grades | Duplex 2205 (UNS S31803/S32205), Super Duplex 2507 (UNS S32750), Lean Duplex 2101 (UNS S32101) |
Composition | Chromium (20-28%), Nickel (1-9%), Molybdenum (0.05-5%), Nitrogen, with other elements like Iron, Manganese, and Copper |
Diameter Range | Typically from 6mm to 200mm (varies per application) |
Tensile Strength | Varies by grade |
- Duplex 2205: ~620 MPa | |
- Super Duplex 2507: ~795 MPa | |
- Lean Duplex 2101: ~600 MPa | |
Yield Strength | Varies by grade |
- Duplex 2205: ~450 MPa | |
- Super Duplex 2507: ~550 MPa | |
- Lean Duplex 2101: ~450 MPa | |
Hardness | Varies by grade and heat treatment |
- Duplex 2205: ~293 HB | |
- Super Duplex 2507: ~310 HB | |
- Lean Duplex 2101: ~290 HB | |
Elongation | Varies by grade |
- Duplex 2205: ~25% | |
- Super Duplex 2507: ~25% | |
- Lean Duplex 2101: ~30% | |
Temperature Resistance | Excellent up to moderate temperatures, limited use at high temperatures due to risk of embrittlement |
Corrosion Resistance | Excellent, particularly against chloride-induced stress corrosion cracking and pitting |
Creep Resistance | Good |
Formability | Good, but less than austenitic stainless steels due to higher strength |
Weldability | Generally good, but requires specific techniques to avoid weld issues |
Applications | Chemical processing, oil and gas, marine, pulp and paper, desalination |
Standard Specifications | ASTM A789, ASTM A790, EN 10216-5, ASME SA-789, etc. |
Stainless steel are manufactured either by hot rolling or cold drawing. They come in various shapes and sizes round, square & hex depending upon its use. These bars are used for its strength and corrosion resistance. The bars are most commonly used for manufacturing of valves, shafts, machine tools, fasteners. It is also used in various industry like shipbuilding, defence, cement, fertilizers, paper & pulp, medical, earth moving equipment, construction etc.
Standard | ASTM A276 / ASME SA276 |
Size | 5mm – 250mm |
Grade | 304, 304L, 304H, 310, 310S, 316, 316L, 316ti, 317, 317L, 321, 347, 904L, SMO254 |
Type | Round, Square, Hex |
Form | Straight , Coil |
Finish | Bright |
Length | upto 6000mm, Cut Length |
Alloy steel round bars are made from steel that has been alloyed with various elements to improve mechanical properties such as strength, toughness, hardness, wear resistance, and corrosion resistance. These bars are used in a wide range of applications, including automotive, aerospace, construction, and heavy machinery. The addition of alloying elements like chromium, molybdenum, vanadium, nickel, and manganese imparts specific characteristics to the steel.
F11 alloy steel round bars are commonly used in high-temperature service applications such as in power plants, refineries, and chemical industries. They are suitable for fittings, valves, flanges, and other components where moderate strength and corrosion resistance at elevated temperatures are required.
F22 alloy steel round bars are used similarly to F11, but they offer higher strength and better corrosion resistance due to increased chromium and molybdenum content. They are suitable for applications in high-temperature environments such as power generation, petrochemical plants, and oil and gas industries.
Property | Specification |
---|---|
Material | Alloy Steel |
Common Grades | 4140, 4340, 6150, 8620, 8640, 52100, etc. |
Composition | Varies by grade, typically includes elements like Chromium, Molybdenum, Nickel, Manganese, Vanadium, Silicon |
Diameter Range | Typically from 6mm to 200mm (varies per application) |
Tensile Strength | Varies by grade |
- 4140: ~655 MPa to 1080 MPa | |
- 4340: ~745 MPa to 1220 MPa | |
- 6150: ~760 MPa to 1230 MPa | |
- 8620: ~620 MPa to 940 MPa | |
Yield Strength | Varies by grade |
- 4140: ~415 MPa to 965 MPa | |
- 4340: ~470 MPa to 1030 MPa | |
- 6150: ~635 MPa to 1080 MPa | |
- 8620: ~345 MPa to 620 MPa | |
Hardness | Varies by grade and heat treatment |
- 4140: ~197 to 320 HB | |
- 4340: ~217 to 352 HB | |
- 6150: ~217 to 302 HB | |
- 8620: ~149 to 255 HB | |
Elongation | Varies by grade |
- 4140: ~18% to 25% | |
- 4340: ~10% to 22% | |
- 6150: ~12% to 18% | |
- 8620: ~16% to 28% | |
Temperature Resistance | Good, suitable for high-temperature applications |
Corrosion Resistance | Moderate, can be enhanced with coatings and treatments |
Creep Resistance | Good |
Formability | Good, varies with grade and heat treatment |
Weldability | Generally good, but requires specific techniques depending on the alloy |
Applications | Automotive, aerospace, construction, heavy machinery, oil and gas |
Standard Specifications | ASTM A29, ASTM A322, ASTM A355, ASTM A434, etc. |
Property | Alloy Steel Round Bar F11 | Alloy Steel Round Bar F22 |
---|---|---|
Material | Chromium-Molybdenum Alloy Steel (UNS K11597) | Chromium-Molybdenum Alloy Steel (UNS K21590) |
Standard | ASTM A182 | ASTM A182 |
Chemical Composition | C: 0.05-0.15%, Mn: 0.30-0.60%, P: 0.040% max, S: 0.040% max, | C: 0.05-0.15%, Mn: 0.30-0.60%, P: 0.040% max, S: 0.040% max, |
Si: 0.50-1.00%, Cr: 1.00-1.50%, Mo: 0.44-0.65% | Si: 0.50-1.00%, Cr: 2.00-2.50%, Mo: 0.87-1.13% | |
Tensile Strength | 415-585 MPa (60-85 ksi) | 415-585 MPa (60-85 ksi) |
Yield Strength | ≥ 205 MPa (≥ 30 ksi) | ≥ 205 MPa (≥ 30 ksi) |
Elongation | ≥ 20% | ≥ 20% |
Hardness (HB) | 187-229 HB | 187-229 HB |
Applications | Power generation, refineries, chemical industries | Power generation, petrochemical plants, oil and gas industries |
Features | Moderate strength and corrosion resistance at elevated temperatures | Higher strength and better corrosion resistance due to increased Cr and Mo content |
Diameter Range | Typically 6 mm to 300 mm (custom sizes available) | Typically 6 mm to 300 mm (custom sizes available) |
Length | 3 meters to 6 meters (custom lengths available) | 3 meters to 6 meters (custom lengths available) |
Carbon steel round bars are made from carbon steel, which is an alloy of iron and carbon. These
bars are commonly used in various industries due to their versatility, strength, and affordability.
Carbon steel round bars are available in different grades, each suited to specific applications
and offering distinct mechanical properties.
Carbon steel round bars can be hot worked to achieve desired shapes and properties.
Property | Specification |
---|---|
Material | Carbon Steel |
Common Grades | A36, 1018, 1045, 1060, 1095 |
Composition | Iron with varying carbon content (up to 2.1%), with small amounts of manganese, silicon, and other elements |
Diameter Range | Typically from 6mm to 200mm (varies per application) |
Tensile Strength | Varies by grade |
- A36: ~400 MPa | |
- 1018: ~440 MPa | |
- 1045: ~585 MPa | |
- 1060: ~620 MPa | |
- 1095: ~850 MPa | |
Yield Strength | Varies by grade |
Aluminum round bars are widely used in various industries due to their excellent properties,
including low density, high strength-to-weight ratio, excellent corrosion resistance, and good
machinability. They are available in various grades and tempers, making them suitable for a wide
range of applications.
Aluminum has a low density, making it ideal for applications where weight is a critical factor.
Aluminum round bars can be hot worked to form various shapes.
Property | Specification |
---|---|
Material | Aluminum |
Common Grades | 6061, 6063, 7075, 2024, 1100 |
Composition | Varies by grade, typically includes elements like Magnesium, Silicon, Copper, Zinc |
Diameter Range | Typically from 6mm to 200mm (varies per application) |
Tensile Strength | Varies by grade and temper |
- 6061-T6: ~310 MPa | |
- 6063-T6: ~240 MPa | |
- 7075-T6: ~570 MPa | |
- 2024-T3: ~470 MPa | |
- 1100-H14: ~110 MPa | |
Yield Strength | Varies by grade and temper |
- 6061-T6: ~275 MPa | |
- 6063-T6: ~210 MPa | |
- 7075-T6: ~505 MPa | |
- 2024-T3: ~325 MPa | |
- 1100-H14: ~105 MPa | |
Hardness | Varies by grade and heat treatment |
- 6061-T6: ~95 HB | |
- 6063-T6: ~73 HB | |
- 7075-T6: ~150 HB | |
- 2024-T3: ~120 HB | |
- 1100-H14: ~35 HB | |
Elongation | Varies by grade and temper |
- 6061-T6: ~12% | |
- 6063-T6: ~12% | |
- 7075-T6: ~11% | |
- 2024-T3: ~20% | |
- 1100-H14: ~25% | |
Thermal Conductivity | Excellent |
- 6061: ~167 W/m·K | |
- 6063: ~201 W/m·K | |
- 7075: ~130 W/m·K | |
- 2024: ~121 W/m·K | |
- 1100: ~222 W/m·K | |
Corrosion Resistance | Excellent, especially with protective coatings and anodizing |
Machinability | Good, especially in grades like 6061 and 2024 |
Weldability | Generally good, with specific techniques for each grade |
Applications | Aerospace, automotive, construction, marine, general engineering |
Standard Specifications | ASTM B211, AMS-QQ-A-225, ASTM B221, etc. |
Titanium round bars are popular materials known for their exceptional strength-to-weight ratio,
corrosion resistance, and biocompatibility. These bars are widely used in industries such as
aerospace, medical, marine, and chemical processing where high-performance and durability are
crucial.
Titanium offers high strength comparable to steel but with approximately half the density, making
it ideal for lightweight applications.
Titanium round bars can be hot worked at elevated temperatures to achieve specific shapes.
Property | Specification |
---|---|
Material | Titanium |
Common Grades | Grade 2, Grade 5 (Ti-6Al-4V), Grade 7, Grade 23 (Ti-6Al-4V ELI) |
Composition | Primarily Titanium with small amounts of alloying elements like Aluminum, Vanadium, and others |
Diameter Range | Typically from 6mm to 200mm (varies per application) |
Tensile Strength | Varies by grade and condition |
- Grade 2: ~370 MPa to 540 MPa | |
- Grade 5: ~895 MPa to 1100 MPa | |
- Grade 7: ~345 MPa to 600 MPa | |
- Grade 23: ~860 MPa to 1100 MPa | |
Yield Strength | Varies by grade and condition |
- Grade 2: ~275 MPa to 450 MPa | |
- Grade 5: ~830 MPa to 1000 MPa | |
- Grade 7: ~240 MPa to 460 MPa | |
- Grade 23: ~800 MPa to 1000 MPa | |
Hardness | Varies by grade and condition |
- Grade 2: ~120 HB | |
- Grade 5: ~334 HB | |
- Grade 7: ~116 HB | |
- Grade 23: ~334 HB | |
Elongation | Varies by grade and condition |
- Grade 2: ~20% to 25% | |
- Grade 5: ~10% to 15% | |
- Grade 7: ~20% to 25% | |
- Grade 23: ~10% to 15% | |
Thermal Conductivity | Low but varies with alloy composition |
- Grade 2: ~20 W/m·K | |
- Grade 5: ~6 W/m·K | |
- Grade 7: ~20 W/m·K | |
- Grade 23: ~6 W/m·K | |
Corrosion Resistance | Excellent in various environments, including seawater and chemical solutions |
Machinability | Relatively good, especially in annealed or solution-treated conditions |
Weldability | Generally good, with specific techniques for each grade |
Applications | Aerospace, medical, marine, chemical processing, sports equipment |
Standard Specifications | ASTM B348, ASTM F136, AMS 4928, MIL-T-9047, etc. |
Nimonic alloys are primarily composed of nickel and chromium, with additions of other elements
such as cobalt, titanium, aluminum, and molybdenum to enhance specific properties.
Nimonic 75: Nickel-chromium alloy with good corrosion and oxidation resistance, used in gas
turbine engineering.
Nimonic 80A: Nickel-chromium alloy with titanium and aluminum, known for high strength and
resistance to high-temperature oxidation.
Nimonic 90: Nickel-chromium-cobalt alloy with titanium and aluminum, used in high-stress,
high-temperature applications.
Nimonic 105: Enhanced version with higher strength at elevated temperatures, used in advanced
aerospace and turbine applications.
Property | Specification |
---|---|
Material | Nimonic |
Common Grades | Nimonic 75, Nimonic 80A, Nimonic 90, Nimonic 105, Nimonic 263, Nimonic 901 |
Composition | Nickel (Ni), Chromium (Cr), Cobalt (Co), Titanium (Ti), Aluminum (Al), and other alloying elements |
Diameter Range | Typically from 6mm to 200mm (varies per application) |
Tensile Strength | Varies by grade |
- Nimonic 75: ~700 MPa | |
- Nimonic 80A: ~850 MPa | |
- Nimonic 90: ~1000 MPa | |
- Nimonic 105: ~1200 MPa | |
- Nimonic 263: ~1200 MPa | |
- Nimonic 901: ~1000 MPa | |
Yield Strength | Varies by grade |
- Nimonic 75: ~300 MPa | |
- Nimonic 80A: ~550 MPa | |
- Nimonic 90: ~550 MPa | |
- Nimonic 105: ~800 MPa | |
- Nimonic 263: ~550 MPa | |
- Nimonic 901: ~400 MPa | |
Hardness | Varies by grade and heat treatment |
- Nimonic 75: ~200 HB | |
- Nimonic 80A: ~240 HB | |
- Nimonic 90: ~220 HB | |
- Nimonic 105: ~250 HB | |
- Nimonic 263: ~260 HB | |
- Nimonic 901: ~240 HB | |
Elongation | Varies by grade |
- Nimonic 75: ~40% | |
- Nimonic 80A: ~30% | |
- Nimonic 90: ~25% | |
- Nimonic 105: ~20% | |
- Nimonic 263: ~20% | |
- Nimonic 901: ~15% | |
Temperature Resistance | Excellent up to high temperatures, suitable for high-temperature applications |
Corrosion Resistance | Good resistance to oxidation and corrosion |
Creep Resistance | Excellent at elevated temperatures |
Formability | Good, but less than some other nickel alloys |
Weldability | Generally good, with specific welding techniques required for optimal results |
Applications | Gas turbine components, aerospace components, high-temperature fasteners, exhaust valves, turbine blades |
Standard Specifications | AMS 5666, BS HR 403, BS HR 501, DIN 17742, UNS N07080, UNS N07090, UNS N07091, UNS N07093, UNS N07263, UNS N09901, ASTM B637 |
Copper bars are essential elements in any earthing and grounding applications as well as in power applications. Copper bars are popular because they withstand harsh conditions and have strong thermal & electrical conductivity. They are also corrosion resistant and are widely used and are often found on switchboards and industrial electrical installations. While copper has been used as currency over the centuries, it has been a primary tool in construction as well. Copper bars application & uses are in various industries like construction, electrical, marine, engineering, defence, HVAC, aviation, railways etc.
Grade | ASTM/EN Standard | Diameter (mm) | Length (mm) | Temper | Surface Finish | Applications |
---|---|---|---|---|---|---|
C11000 (Electrolytic Tough Pitch Copper) | ASTM B187 / B187M, EN 13601 | 3 - 200 | Up to 6000 | H04 (hard), H02 (half-hard), M20 (annealed) | Mill finish, polished | Electrical applications, bus bars, transformers |
C10100 (Oxygen-Free Copper) | ASTM B187 / B187M, EN 13601 | 3 - 150 | Up to 6000 | H04 (hard), H02 (half-hard), M20 (annealed) | Mill finish, polished | High conductivity applications, semiconductors, vacuum seals |
C12200 (Phosphorus Deoxidized Copper) | ASTM B187 / B187M, EN 13601 | 3 - 150 | Up to 6000 | H04 (hard), H02 (half-hard), M20 (annealed) | Mill finish, polished | Plumbing, HVAC, heat exchangers |
C14500 (Tellurium Copper) | ASTM B301 / B301M, EN 13601 | 3 - 100 | Up to 6000 | H04 (hard), H02 (half-hard), M20 (annealed) | Mill finish, polished | Machining applications, electrical connectors, fasteners |
Brass bars are the most widely used and least expensive of copper-based alloys. Brass is a popular material for moving parts because of its low surface friction and is available in various grades and bar shapes. They are relatively good corrosion resistant, moderately high strength, and in some compositions exceptionally good ductility and excellent forming characteristics when shaped by pressing, deep drawing, rolling and machining. Brass has a high tensile strength and is easy to machine and are used in making machine parts, gear boxes, valves, bearings, aircraft components, shafts of propeller & bushings.
Grade | ASTM/EN Standard | Diameter (mm) | Length (mm) | Temper | Surface Finish | Applications |
---|---|---|---|---|---|---|
C36000 (Free Cutting Brass) | ASTM B16 / B16M, EN 12164 | 3 - 100 | Up to 6000 | H02 (half-hard), H04 (hard) | Mill finish, polished | Machining applications, fasteners, fittings |
C38500 (Architectural Bronze) | ASTM B455, EN 12164 | 3 - 100 | Up to 6000 | H02 (half-hard), H04 (hard) | Mill finish, polished | Decorative applications, architectural hardware, trims |
C26000 (Cartridge Brass) | ASTM B16 / B16M, EN 12164 | 3 - 150 | Up to 6000 | H02 (half-hard), H04 (hard) | Mill finish, polished | Ammunition casings, hardware, electrical components |
C33000 (Low Leaded Brass) | ASTM B135, EN 12164 | 3 - 150 | Up to 6000 | H02 (half-hard), H04 (hard) | Mill finish, polished | Plumbing fittings, valves, low-lead applications |